VDL Special Vehicles continues to innovate factory
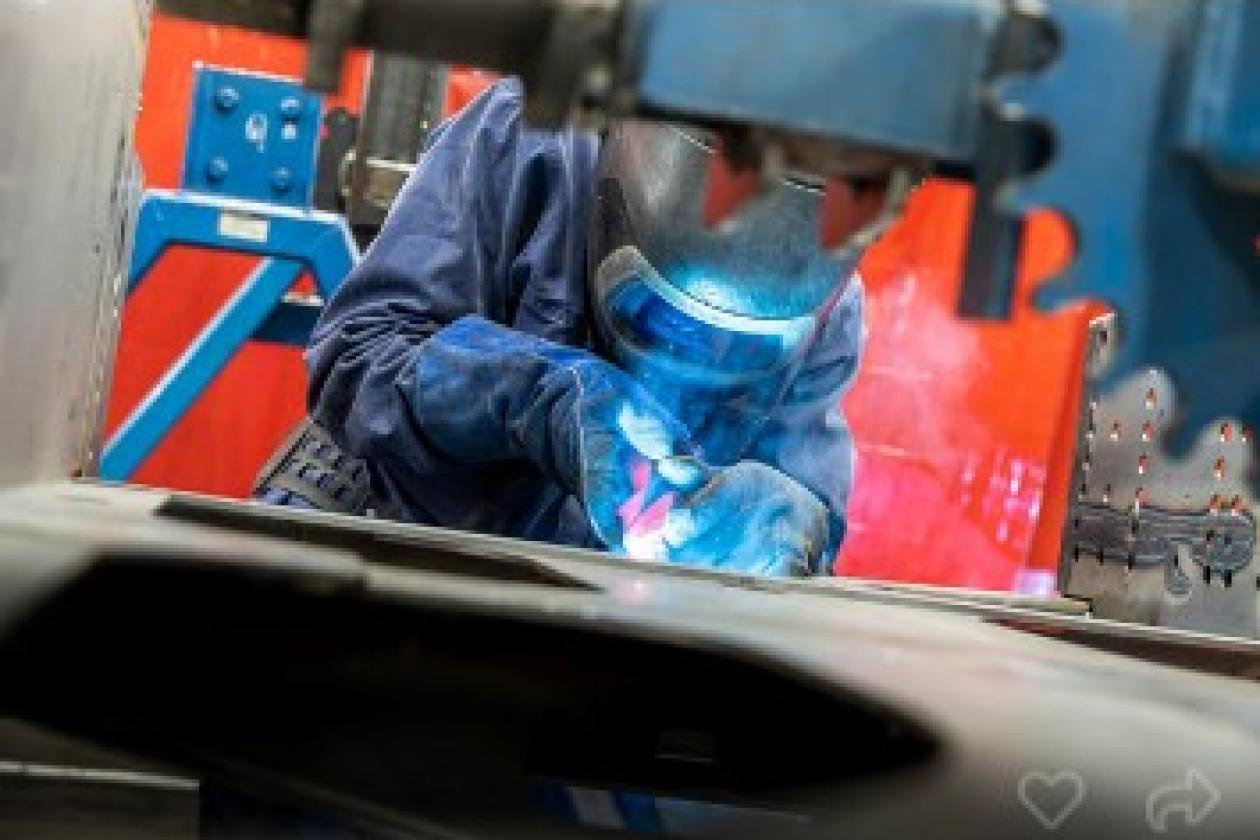
When installing the latest technologies such as electrification and hydrogen fuel cells in on- and off-road vehicles, it is naturally important to keep up with new technologies in terms of production. VDL Special Vehicles is therefore continuously renewing and innovating the production process, in order to always be able to apply the latest zero-emission technology and optimize the production process. This enables VDL Special Vehicles to guarantee constant quality and speed up project lead times.
New welding robot: rotary table
For smaller parts, sub-assemblies or products of up to 2.5 meters, a robot installation with turntable from Yaskawa is currently being installed. This is a "small" welding robot which welds sub-assemblies. "Small" is relative because the turntable still takes up about 35 m2 of space. Tryouts were held with the robot in January. In February, the welding robot will go into production.
Currently a lot of welding is outsourced. With this robot installation, that will become a thing of the past and VDL Special Vehicles will be able to produce much more in-house. The robot welds two to three times faster than can currently be achieved with manual welding. The robot's repetitive actions ensure constant quality and reproducibility and increase output.
Assembly continues to be performed manually using advanced (poke yoke) suture jigs. Programming is done 100% offline with Delfoi's programming package. Programs and parameters are optimized at the robot with the tech pendant (the controller to control the robot). Because it works with a rotary table, the operator can load the empty station while the robot is running production on the other station.
Not only for the installation of this welding robot was part of the factory hall redesigned. But also because of the logic of the work flow, storage and expedition were moved to another part of the building. This adjustment allows us to minimize the number of transport movements. When installing the welding robot, a spot extractor was used since it is a compact cell with complete enclosure. This ensures that emissions are extracted 100% at the source.
Current welding line under development
To be able to guarantee increasing demand and continuous quality VDL Special Vehicles is developing two complete welding lines. In cooperation with the firms Valk Welding B.V. and Kuunders Technoworks B.V., two welding lines have been developed with one welding robot installation in each line. The modules can be loaded, welded and emptied unmanned for at least one shift (8 hours). The new welding lines will provide the necessary time savings.
The line will be set up more efficiently so that the work sequence is a logical one: entry - bonding - finishing welding - finishing to measuring. A number of molds have already been developed and delivered. These molds are constructed so that the modules are produced first time right and reproducibility is guaranteed.
The first welding line involves a conversion of the current welding robot installation. In order to load it unmanned, the modules will be supplied by means of a conveyor belt. This modification will make the current welding robot installation 35% faster. The space created by this modification will be used for the second robot line.
At the second welding line, in addition to new jigs, a complete new welding robot installation is being installed. This installation consists of a gallows with 2 suspended robots on it, which allows us to weld 35% faster and more symmetrically. The latter ensures that modules distort less. Here too, the modules are loaded, welded and emptied unmanned.
Because of this automation, we are training and educating our employees on programming, maintenance, troubleshooting. The employees can also help with the development of molds. Because the numbers are going to increase in the coming years and we are also going to make all the sub-assemblies in-house, this automation will not affect the number of jobs. On the contrary, we need more people!